
Published in the July/August 2020 Issue – SE Asian shipyards, traditionally smaller, look to build affordable vessels but may face economic peril in the post-COVID-19 world.
Efforts to improve naval shipbuilding capacity are mixed across the Indo-Pacific region and depend largely on the naval shipbuilding programmes that are underway or planned. Some countries are developing ship programmes because of increased threats in the maritime domain, but most want to get industrial self-reliance in an area that can boost the economy, create jobs and bring in technology as well as help project status internationally.
Dr Collin Koh Swee Lean, from the Institute of Defence and Strategic Studies at the S. Rajaratnam School of International Studies (RSIS) in Singapore told AMR: “Most of the Indo-Pacific region’s modern shipyards are found in Northeast Asia, such as in China, Japan and South Korea. In the Oceania, we’ve Australia. In South Asia, there’s India. In Southeast Asia, Indonesia, Malaysia, Singapore, Thailand and Vietnam possess the region’s most modern shipbuilding capacities.”
He added: Myanmar is one example that’s often ignored, though the growth of its naval shipbuilding capacity is geared towards meeting domestic needs. Still, in the long run, the capacity could position the country well for export prospects. And so is the case of Bangladesh, which is clearly also looking at export opportunities.
Collins said that that in South East Asia the enhancement of shipyards has been ‘minimal’ with ‘perhaps the exception of Indonesia which has recently acquired the capacity to build its first submarine under DSME licence.
In South East Asia there are shipbuilding programmes underway that centre on OPVs and frigates. The main OPV programmes are being undertaken by the Song Thu Group in Vietnam; by Destini/THHE in Malaysia; Bangkok Dock in Thailand; and both PT Citra and PT Malindo in Indonesia. In South Asia the Thanlyin shipyard in Myanmar is building new OPVs and in Bangladesh there are signs that naval shipbuilding capacity is being expanded at Khulna Shipyard.
OPVs are the simplest of naval vessels to build and these countries are able to use their existing commercial shipbuilding facilities to undertake OPV projects. More complex warships like frigates are much harder to construct. Malaysia is pushing ahead with frigate construction at Boustead Naval Shipyard, in Indonesia this capability is being centred upon PT Pal, and in Pakistan Karachi Shipyards is undertaking frigate construction too. But all are being undertaken with the assistance from overseas companies with a significant degree of technology transfer.
Collin said: “Generally across the Indo-Pacific, OPVs and frigates are areas of focus because of not only domestic maritime forces imperatives but also for export prospects. These assets tend to be popular on the international naval market, more affordable for more navies and coastguards. The trend towards OPV, is the result of a general proliferation trend for maritime law enforcement agencies, especially in the Indo-Pacific where there’s a considerable market for such vessels. But in Northeast Asia, there are not only OPVs and frigates, but destroyer programmes also in vogue.”
Technology transfer has been required to enable shipyards to embark on these projects. The main challenge has less to do with precision machinery that can be acquired commercially but more related to systems integration.
“This is a major hurdle those lesser shipbuilders in the region have to overcome and this is only possible through technology transfer,” Collins said, “The other challenge is manpower – not just skilled welders and draftsmen, but also the engineers. They have to be adequately trained, and able to ensure quality control in the shipbuilding process.”
Damen Schelde Naval Shipbuilding (DSNS) has been one of the more successful companies in the region and is assisting several yards in Vietnam and Malaysia’s Destini with OPV programmes and PT Pal in Indonesia with the construction of frigates.
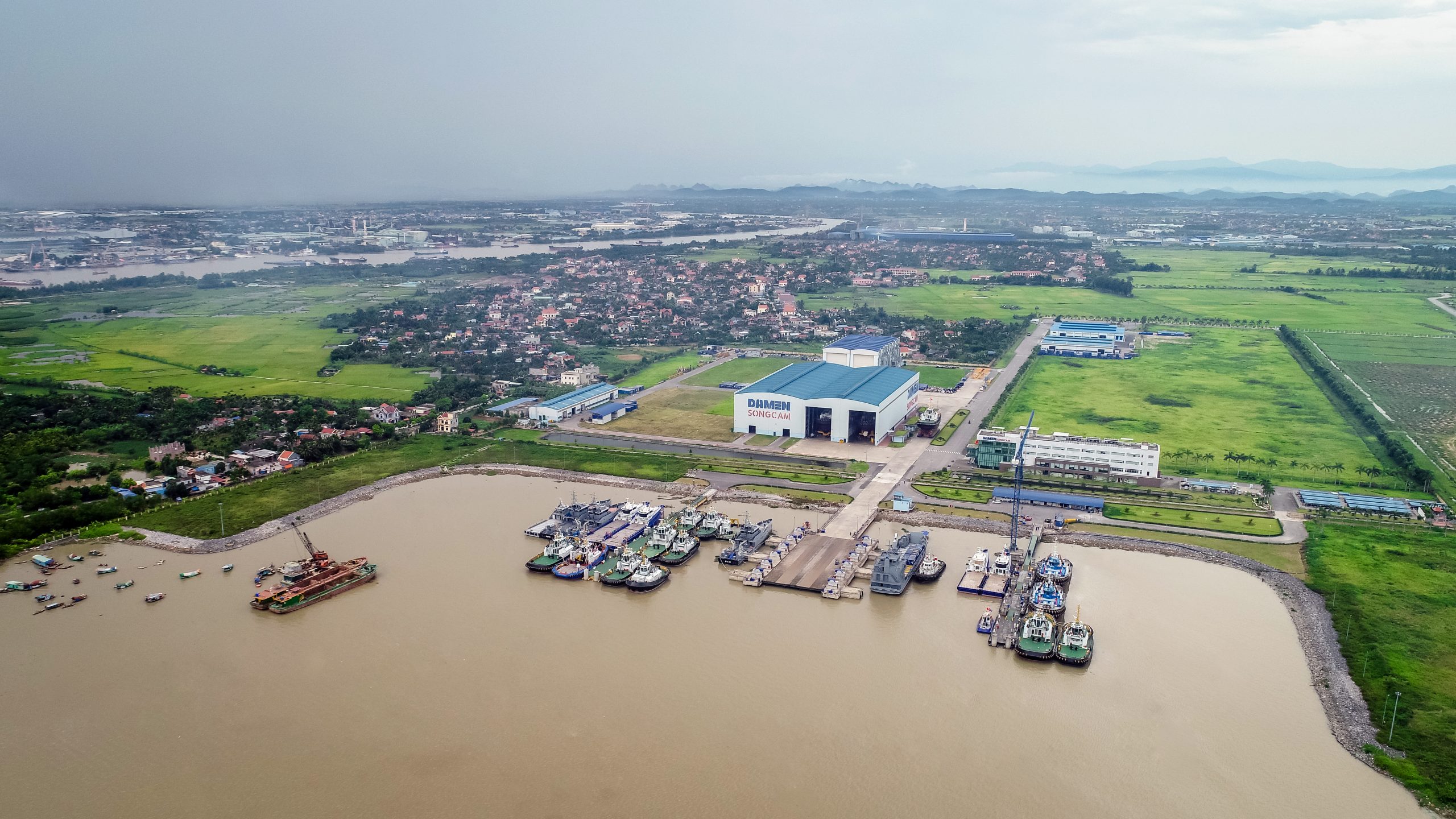
Roland Briene, commercial director at the company told AMR that DSNS helped the shipyards with both infrastructure requirements and technology transfer.
“In most cases the facilities were already there but they usually need some minor modification,” he said. Modifications were discussed with the shipyards and would reflect the building strategy for the ships. “The building strategy has to be aligned with the infrastructure, what kind of launch, what kind of transfer of blocks on the premises of the shipyard is needed. If that means extension of sheds or an extra loader to carry blocks around the yard or different welding machines that will be discussed, that is the kind of advice we provide. Those are key elements, the bigger the project the more tailored it gets,” Briene added.
In Vietnam DSNS’s partner yard in Haiphong required an extension of its sheds and improved storage facilities considering the sensitivity and complexity of naval vessels. “If you bring sensors and weapons to the shipyard they need to be stored in a preserved way in terms of temperature and humidity and that is what we had to build with the yard,” Briene explained.
In Indonesia, PT Pal had the necessary infrastructure and it was more about delivering specific skills that would enable a transition from commercial ships to frigate construction. Here, Briene said that one area of focus was the upgrade in welding skills and equipment specific for that project.
“If you build tankers and now go to navy ships the steel plate thickness is much less, it is not a heavy steel welding that you are used to you need more specialised welding. Also if you have to install sensitive sensors and radar systems that are not on container ships, that requires an upgrade of those skills too. We provide them with that,” he said.
This is the kind of mix of assistance that is required to develop shipyards in the region and depends largely on the scale of the project and the existing facilities and skills sets. But bringing in technology is not always a simple process. Collin said that whilst it is very important recipient countries “need to create the necessary domestic conditions for technology transfer to be effective. This includes creating the regulatory frameworks or policies to make it effective and efficient, and also, the requisite human capital.”
In addition he said that there that are some local shipbuilders that aren’t necessarily satisfied with the extent of technology collaboration with foreign vendors, “with some complaining that they are denied full access to the requisite tech, or not fulfilling contractual terms on transfer of technology generally.”
But the outlook looks bleak following the COVID-19 pandemic. Spending on health and other social and economic programmes means that the outlook for navies is uncertain. Collin said that if demand for maritime forces could be undermined and this in turn will affect the shipbuilding developments.
“The smaller players will be amongst the hardest hit, whereas the larger and more established ones in the region could more or less stay buoyant with sufficient government intervention and support,” he said. “We’ll be lucky if we see the existing ones remaining intact long after the pandemic and its economic fallout, which could result in complete shutdowns or mergers and consolidation.”
by Tim Fish